
Innovative Designs for your future website
At the heart of our work is the desire to build clean, functional, and stunning websites. Whether you're a small business or a growing brand, we transform ideas into fast, user-friendly digital spaces that make an impact.
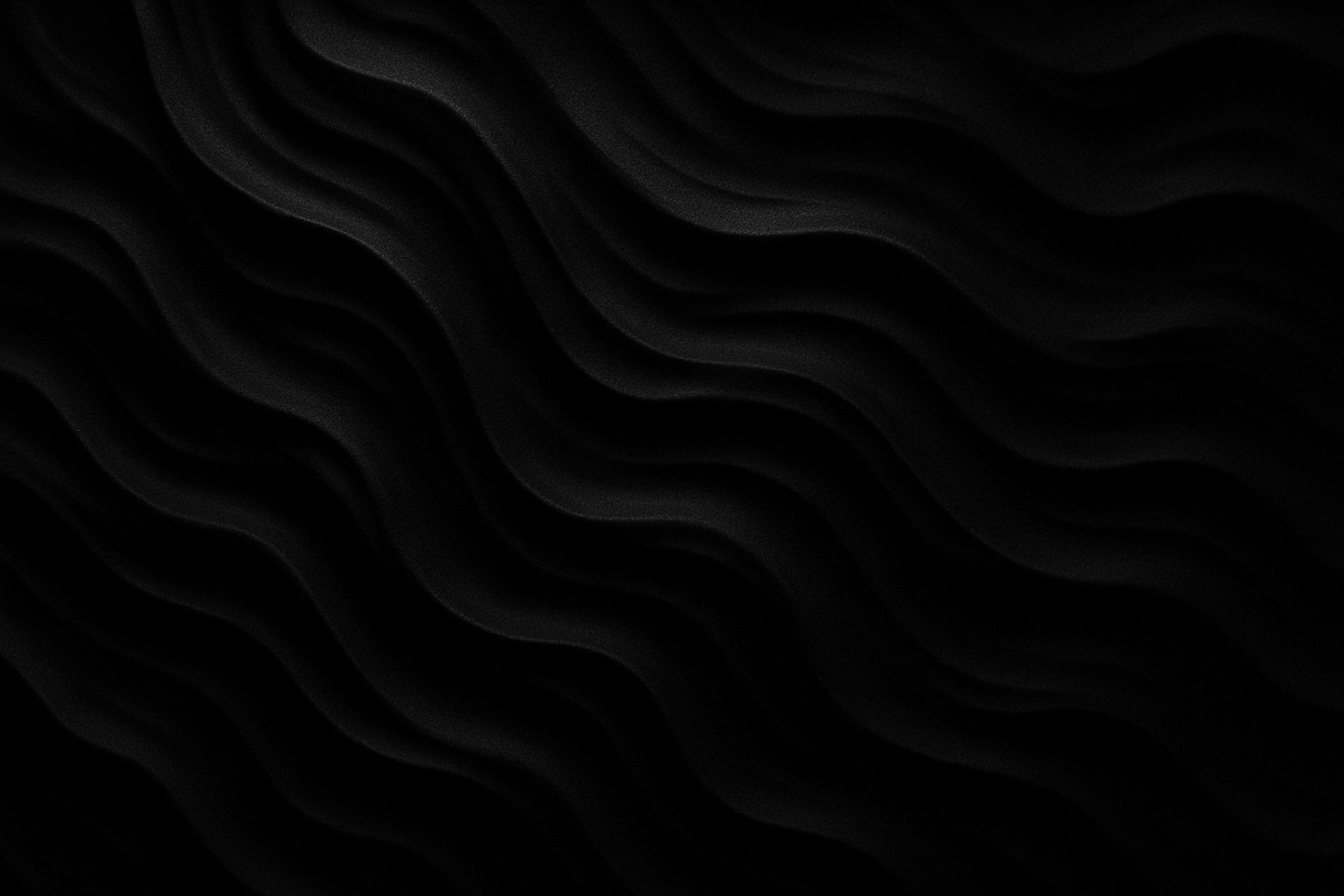
Designed for Impact
Explore innovative designs that redefine our website creation
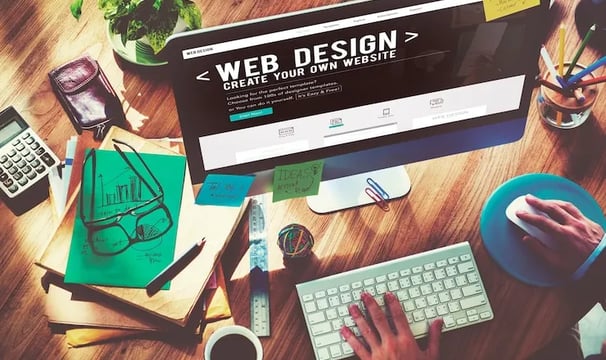
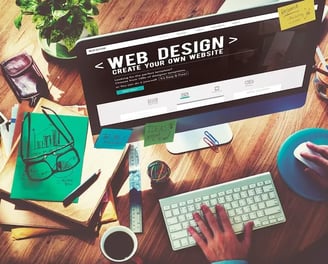
Creative Strategy
We blend creativity with strategic thinking to build digital experiences that are as smart as they are stunning. Every site we create is rooted in user experience, with tailored layouts and clear messaging that connect brands to audiences in meaningful ways.
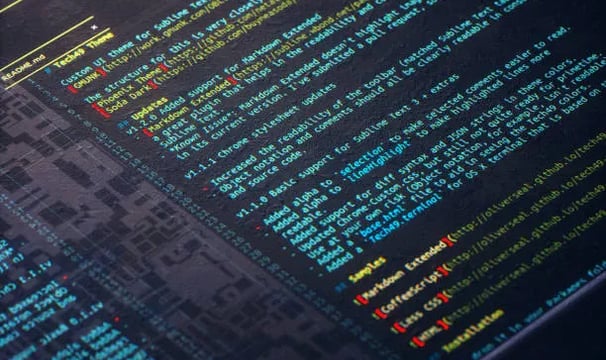
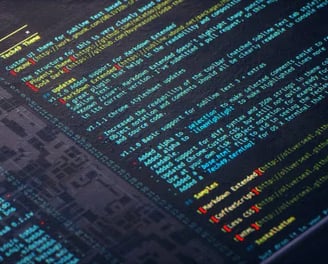
Clean, Scalable Code
Our developers build fast, responsive, and secure websites using modern frameworks and best practices. From landing pages to complex platforms, we write clean code that scales with your business and adapts to any device.
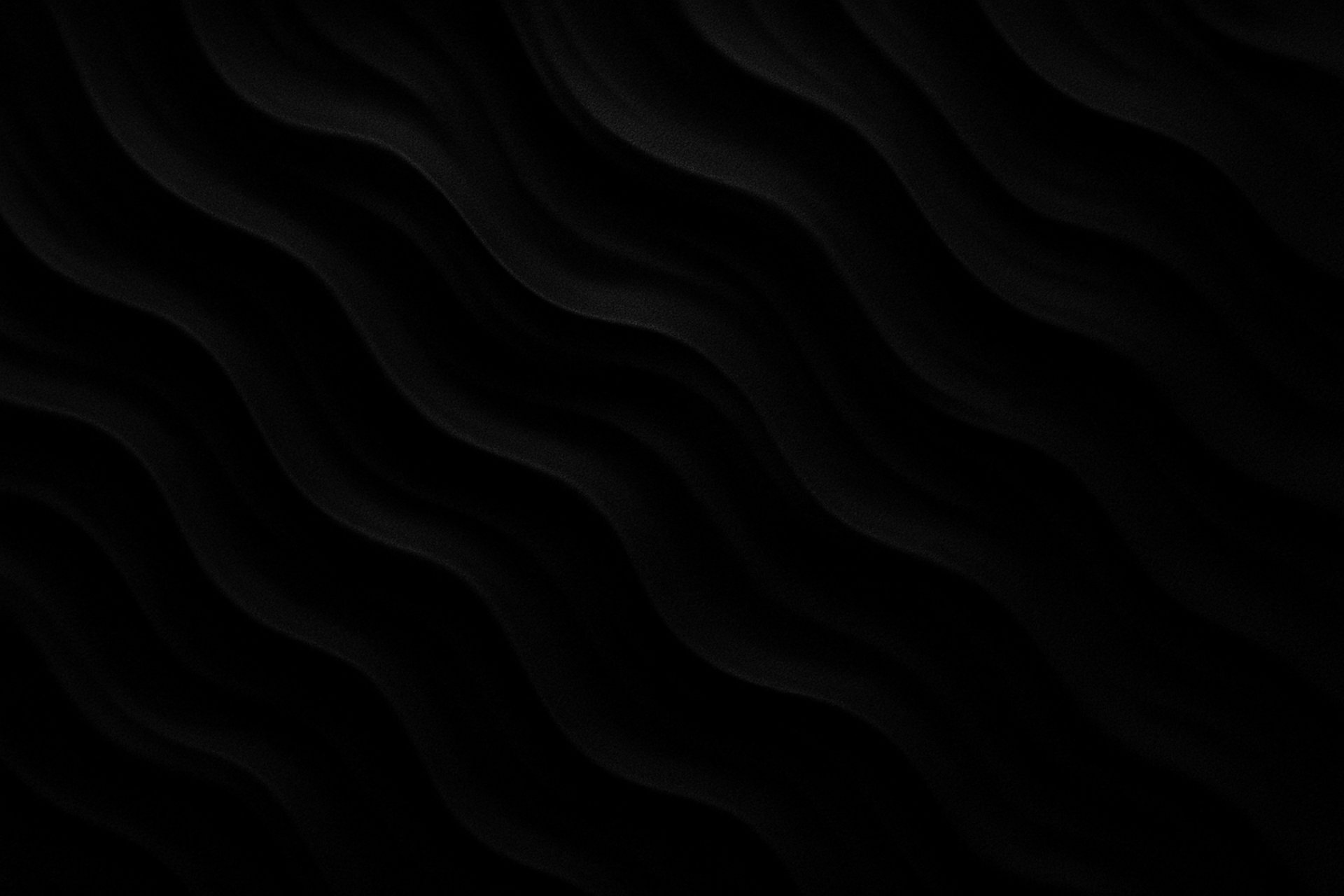
Website Development Services
Transforming spaces with innovative and modern website solutions tailored to your needs.
Full Develop Package Services
For businesses ready to make a bold digital impact, our Full Develop Package offers a complete end-to-end solution. From initial planning and UI/UX design to custom development, SEO setup, and deployment, we’ll handle every step.
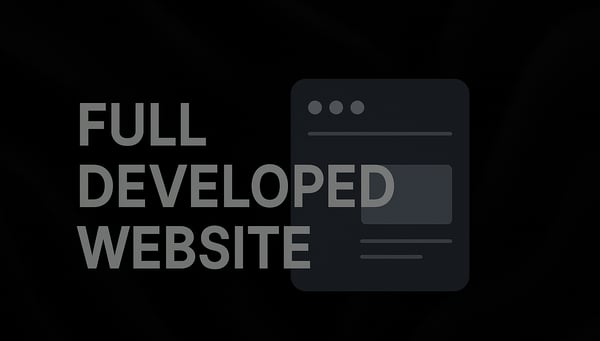
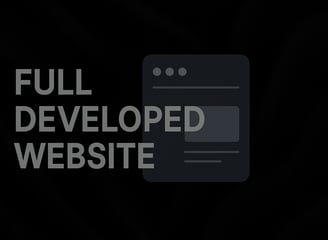
Pay per Page Services
Need a quick, custom solution without committing to a full website build? Our Pay per Page service offers a flexible, budget-friendly option for clients who want to develop their websites one page at a time.
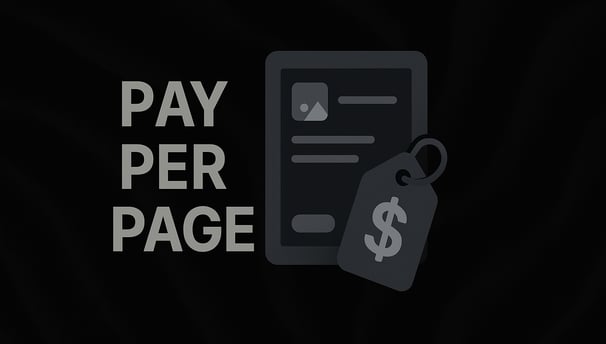
